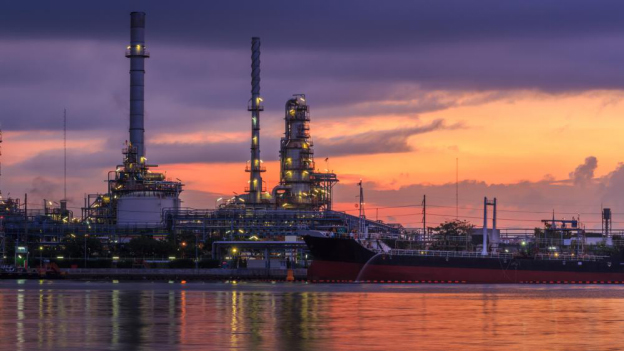
Our loss prevention engineering services includes development and implementation of process safety management system, technical safety studies for both green and brown field projects, preparation of a project specific fire and safety philosophy, fire water system design, fire and gas detector layout and any client specific design requirements.
Haneon Fort Engineering Company Limited offers a complete suite of loss prevention engineering which spans process safety, fire engineering and risk management services. Designed to accommodate every client’s specific project needs, our loss prevention designs and execution comply with the latest engineering codes, standards and industry best practices.
We offer loss prevention services for both new capital projects and debottlenecking of existing facilities. The scope of our loss prevention services includes, but is not limited to,
- The preparation of a project specific Fire and
- Safety philosophies;
- Fire water system design,
- Fire water demand calculations;
- Relief system sizing,
- Fire and gas Detector Layout and Specification
- Installation of Fire Protection Systems.
Your Health and Safety is Our Priority
Our customized loss prevention solutions take into account the health and safety of your company’s personnel.
Utilizing proven technology, we make sure our solutions do not also compromise the integrity of the environment
Our expertise includes, but is not limited to:
Quantitative Risk Assessments (QRA);
- Fault Tree
- Event Tree
Occupational Health Risk Assessments (OHRA);
Safety Risk Assessment (SRS);
HAZAN / HAZID / LOPA / SIMOPS;
HSEIA;
Bowtie Analysis;
Operating Procedure Review and Development;
Audits against:
- OSHA PSM Standard (29 CFR 1910.119);
- OHSAS 18001;
- NFPA Life Safety 101
PSM programs:
- Process Hazard Analyses (PHAs);
- Layer of Protection Analyses (LOPAs);
- Resolving/Engineering/Implementing PHA recommendations;
- PHA Revalidations
- Safety Integrity Level (SIL) selection analyses for Safety Instrumented Systems (SISs)
- Safety Instrument Function Verification (SIF);
- Layer of Protection Analysis (LOPA);
- Risk Graph;
- PSM Compliance Audits;
- Preliminary Hazard and Operability Studies (HAZOPs);
- New Plant HAZOPs and PHAs;
- PHA facilitation training;
- Management of change;Incident investigation training
Independent program assessments;
Evaluating extent of regulatory coverage and documenting legal justification for coverage boundaries;
Performing hazard assessments
EPA Risk Management Plans
- Plan Development;
- Strategic Planning;
- ompliance Audits;
- Offsite Consequence Analysis;
- Hazards Assessment;
- Emergency Response Programs
- Worst Case Scenario Documentation
- EPA Risk Management Plan Updates
Mechanical Integrity Program Development;
Mechanical Integrity Audits;
Decommissioning Studies;
Facility Siting Analysis and Evaluation;
Pre-Acquisition Due Diligence Surveys;
Operating Procedures Development;
Review or Revalidation of Operating Procedures;
Operator Task Analysis;
Technical Writing; Assistance in abating OSHA citations;
Litigation support and Expert Witness services
Developing Process Safety Information, including
- Process flow diagrams (PFDs);
- Process chemistry;
- Chemical compatibility matrix;
- Maximum Intended Inventories;
- Safe upper and lower operating limits and consequences of deviations;
- Materials of construction;
- Piping and instrumentation diagrams (P&IDs);
- Electrical Classification drawings and interpretation of codes and standards regarding area electrical classification;
- Relief System design and design basis, including determining relief valve sizing bases and evaluating flare header capacity, liquid knockout requirements, and flare stack design for adequacy;
- Ventilation System design information such as compressor building ventilation systems, including interpretation of applicable codes and standards for determining ventilation requirements;
- Identifying design codes and standards employed in the design of a process;
- Material and energy balances;
- Safety systems documentation, including safety system plot plans and written descriptions of safety systems (e.g., interlocks, detection, suppression, utility, and containment systems);
- Identifying recognized and generally accepted good engineering practices used in the design of a process.
Process Safety Management Services;
PHA Facilitation/HAZOPs;
Risk Management Program Development;
Plant Operations Support;
Process Controls Services;
Process Troubleshooting;
Technical Training.